|
|
Lean Leadership Summit: Speaker Bios
The "Rock Stars of Lean!" An absolutely unprecedented assemblage of many of the most capable and successful executive Lean Leaders on the planet in an intimate setting to share how they transformed their operations to create competitive advantage to grow their businesses.
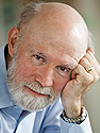 |
|
James P. Womack
Founder and Chairman, Lean Enterprise Institute is the foremost proponent of the Lean Movement
in the world. Jim led the research team for MIT's five year 5 million dollar study of the global
automotive industry which introduced the term "lean". This term describes Toyota's unique business
system that created competitive advantage in product development, supply chain management,
fulfillment from order through production to delivery, customer support and enterprise management.
He is co-author of the The Machine That Changed the World, Lean Thinking, Seeing the Whole, Lean Solutions and numerous articles.
|
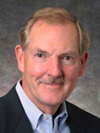 |
|
Gary Convis
Retired Toyota Manufacturing President and current Senior Adviser, Dana Corporation—most senior American executive leading the development of
Toyota's 2.2 million vehicle production and supply base in North America. Learn the secrets of the "NUMMI miracle"—how under Toyota leadership
General Motors' worst plant was transformed into its best. Mr. Convis was hired from Ford to be the senior American executive to lead the launch
of Toyota's first North American manufacturing plant, NUMMI. An effective leader of the Toyota Way, Mr. Convis was promoted to executive vice president
of NUMMI, then president of the largest production site, Toyota Motor Manufacturing Kentucky, with concurrent responsibility as executive vice president
of Toyota Engineering and Manufacturing North America and Managing Officer of Toyota Motor Corporation. Following retirement, he joined Dana Corporation as CEO, moved to Vice Chairman in 2009 and currently serves as Senior Adviser. (Mr. Convis' book will be published by the time of our event.)
|
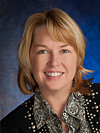 |
|
Virginia (Ginger) Chandler
Vice President of Product Design and Management, Smith and Wesson Corp.
Ginger Chandler is a senior leader with excellent operational skills that she has employed to lead and coach several high-volume manufacturing organizations through significant transformations, and to deliver dramatic improvements across a spectrum of performance metrics.
For ten years at Morton International, Chandler held a series of increasingly responsible positions to ultimately become Process Line Manager for Toyota Module Production within the Automotive Safety Division. Earlier roles at Morton in design engineering, product development, and process redefinition, provided her with the knowledge and experience required to master and to implement a Toyota Production System (TPS) environment. She then joined Breed Technologies, as Vice President of Engineering, where she created and implemented worldwide, concept-to manufacturing, development processes that cut cycle times in half, and improved product quality through enhanced organizational integration. In 1998, Chandler moved to YOMO Consulting, where for seven years she helped a number of world class companies to successfully adopt and implement the Toyota Production System. Clients included, among others, Alcoa, Meridian, Whirpool, Dell Computer, Yazaki, and Advanced Transformer.
Chandler holds a number of patents for her engineering design work within the automotive industry. She received her Bachelor of Science in Mechanical Engineering from Lamar University in Beaumont, Texas.
|
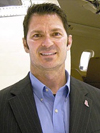 |
|
David Coleal
Vice President and General Manager, Bombardier Aerospace-Learjet—Former Toyota NUMMI manager leads Learjet to top performance of 9 plants worldwide. David brings a style of Lean leadership where he actively seeks involvement and coaches his team to success. His ability to take complex issues and pare it down to manageable attackable pieces allows him to quickly gain momentum across an organization. The envy of many lean leaders. Prior to Learjet, he was COO/Executive VP for Cirrus Design Aviation where he grew the company from $50MM to $300MM in 5 years to become a dominant brand for its class. David was also a consultant for McKinsey & Co. and was a Quality Engineer leader in Toyota NUMMI.
|
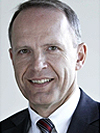 |
|
Otmar Hauck
Otmar Hauck, Chief Operating Officer, KION GROUP, Europe's No. 1 manufacturer for material handling systems explains how Toyota Way thinking was adapted to German company culture.
Otmar joined the Volkswagen Group's Audi Brand in 1986 after 12 years of service in the German Armed Forces and is still proud of his last rank as a Captain. He held several positions in the Audi Human Resources Division and was transferred to the Volkswagen Group's Headquarters in Wolfsburg in 1992. After a short time in Human Resources he joined the Production Division of the Volkswagen Brand. Some of his major responsibilities since then have been Head of Car Assembly in Wolfsburg from 1999 to 2003 and Executive Director of the Car Plant of Volkswagen de Mexico from 2004 to 2007. In both positions he was responsible for the daily production of several thousands of vehicles. His final position at Volkswagen was Executive Director of Volkswagen's Business Unit Plastic.
Since his very first years in production, Otmar has been an eager student and convinced follower of the principles of the Toyota Production System and successfully implemented many of this procedures inside the Volkswagen World. He is now busy to make the KION production system work and grow.
|
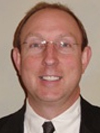 |
|
John Marushin
Director, Alcoa Operations Management System; and former Toyota Supplier Development Manager. To implement Toyota's American supplier development outreach program, John was trained by the Toyota Motor Corporation Japan, as an expert in "Toyota Production System" methodology through actual projects in both North America and Japan. This training was expanded outside of Toyota through consulting engagements spreading the TPS knowledge to companies around the world to enhance their overall operations and their relationships with both customers and shareholders. Leading the "Alcoa Business System" as the Director of Alcoa's Operation Management Consulting group (Global), John has built a sustaining internal consulting organization that has the capability to improve businesses and train others to improving efficiency & productivity. Worked with high level executives to rethink how they run their business to get the most out of the people and operations and to retool their business to compete in a global world of constant competition. Reported directly to Alcoa's Chief Executive Officer to keep him updated on the latest activities and needs from his level to keep the new system moving forward.
|
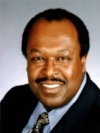 |
|
Fletcher Davidson
Vice President North American Parts Operations, Toyota Motor Sales USA—Leader of the auto industry’s most efficient service parts supply chain (best service with double
the inventory turns and 50% higher labor productivity vs. competitors) explains key factors in achieving these results and the impact on customer loyalty and revenue growth.
For over 30 years, Mr. Davidson has led the development of Toyota's $4 billion North American service parts and accessories supply chain, inventory management systems, and
warehousing and logistics operations as the company transitioned from a small importer to the second largest automobile manufacturer in the North America and the benchmark
of the global industry.
|
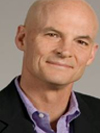 |
|
Dr. Mike Morrison
is a former founder and Vice President for the University of Toyota—a corporate university he helped to launch in 1998. Mike's passion centers on the principles and practices of developing leadership at all levels of an organization. His leadership research and hands-on experience has been documented in two popular books (Leading Through Meaning '03 and The Other Side of the Card '06) and a wide range of publications including the Harvard Business Review. Mike has designed, developed, and managed dozens of high-impact leadership and management development programs.
Mike is also a globally recognized leader in Lean Thinking – with a special focus in applying “LEAN” principles and practices to "service and knowledge worker" environments. He has developed a wide range of education and application strategies that have produced dramatic business results. A key focus is helping organizations move beyond narrow “efficiency” targets, operational excellence, and traditional work cultures—to create broad capacities for continuous improvement, innovation, and world-class performance.
Mike's education has taken him from the liberal arts foundations of Gonzaga University—to a University of Southern California MBA—to a doctoral degree at Claremont Graduate University's Peter F. Drucker School.
|
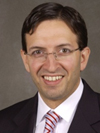 |
|
Amir Dan Rubin
How Lean Thinking raised UCLA Medical Center to top of national rankings. Amir currently serves as Chief Operating Officer (COO) for the UCLA Hospital System, an integrated
academic medical center committed to leading edge research, teaching, and patient care. In his role at UCLA, Amir is responsible for the operations of the Ronald Reagan UCLA
Medical Center, Mattel Children's Hospital at UCLA, the Resnick Neuropsychiatric Hospital at UCLA, Santa Monica-UCLA Medical Center and Orthopedic Hospital, and an array of
outpatient centers across the west side of Los Angeles. Amir oversees an operating budget of $1.4 billion and over 8,000 employees.
During Amir's tenure, UCLA has advanced its performance on quality, safety, service, and operational performance measures. U.S. News & World Report continues to rank UCLA among the top
three hospitals in the nation in its annual rankings. Under Amir's administration, the organization has also transitioned into new state of the art facilities, achieved the highest patient
satisfaction scores in the organization's history, and delivered the best financial performance in the organization's history.
|
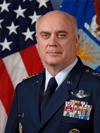 |
|
General Carrol H. (Howie) Chandler
Vice Chief of Staff of the United States Air Force—4-star Commander of the entire Pacific Theater applied Lean
Thinking to totally transform his command's Lean strategic planning and management process. So successful that the
Air Force is now deploying this process globally.
General Chandler is the 35th and current Vice Chief of Staff of the Air Force. As Vice Chief, he presides over the Air Staff and serves as a
member of the Joint Chiefs of Staff Requirements Oversight Council and Deputy Advisory Working Group. He assists the Chief of Staff with organizing,
training, and equipping of 680,000 active-duty, Guard, Reserve and civilian forces serving in the United States and overseas. He previously served as Commander of Pacific Air Forces.
|
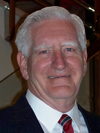 |
|
Keith Turnbull
Keith Turnbull, Retired Executive Vice President of Alcoa and currently Toyota Production System adviser for Giant Eagle Supermarkets. Keith's entire career has been as a change agent: first as a research director, then as corporate strategist and finally as companywide TPS implementer. Nothing has been more noble and more expansive than learning Toyota's System and transitioning it intact out of Toyota into major corporations in businesses vastly different from the auto industry. His sensei has been Hajime Ohba of TSSC, his TPS guide John Marushin, his concurrent learner/doers Kent Bowen and Steve Spear of Harvard, his fellow traveler Vickie Pisowicz. The scope of his travel has been from the minute details of TPS to the board room strategies and culture changes required for Toyota's System. He has "published" his findings in a book, The Alcoa Business System, which is Alcoa proprietary.
|
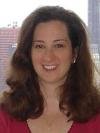 |
|
Vickie Pisowicz
Vickie Pisowicz, Owner of Vickie Pisowicz, LLC consulting company and currently Toyota Production System advisor of Giant Eagle Supermarkets. Vickie has spent the last 14 years applying the principles of the Toyota Production System in various manufacturing and non-manufacturing environments including health care and non-profit agencies. At Alcoa Vickie was introduced to the principles of the Toyota Production System and served as an internal consultant under the leadership of Keith Turnbull. At the request of then Alcoa CEO Paul O'Neill and with the support of the Toyota Supplier Support Center and Kent Bowen of Harvard, Vickie was asked to help apply these system principles in the local health care industry. In addition, she has advised various non-profits such as the Women's Center and Shelter of Greater Pittsburgh, and is currently partnering with Keith Turnbull and Mike Murney in supporting Giant Eagle's company-wide adoption of the Toyota Production System. Vickie holds a Bachelor of Mechanical and Aerospace Engineering from Princeton University, a Master of Business from Harvard Business School, and a Master in Public Policy from the Kennedy School of Government.
|
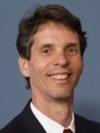 |
|
Mike Hoseus
Mr. Hoseus brings both manufacturing operations and specialization in Human Resource experience to his role as Executive Director for the Center for Quality People & Organizations (CQPO).
CQPO is an organization developed in 1999 as a vision of Toyota Motor Manufacturing to share Lean Quality philosophy and human resource practices with education, business, and
community organizations. CQPO's current projects with Toyota include New Hire selection and training process, Team Leader and Group Leader post-promotion training, Quality Circle Leader and Manager training,
and Global Problem Solving for all levels.
Prior to CQPO, Mike was a corporate leader for 13 years at Toyota Motor Manufacturing's Georgetown, Kentucky plant both in Human Resources and Manufacturing. As Assistant General Manager in
Human Resources, his responsibilities included personnel, safety, HR development, employee relations, benefits, training, and manufacturing/human resource teams for a plant of 8,000 team
members. His major initiative was development of the enhanced relationship between Human Resources and Manufacturing. Mike’s operational responsibilities in manufacturing began with the
start up of the plant in 1987 as front line supervisor in vehicle assembly. This included all aspects of safety, quality, productivity, cost and morale for operations. With experience as
Assembly Plant Manager and eventually Assistant General Manager, his responsibilities increased to include both assembly plants including operations, maintenance, and engineering. He is a
Toyota Certified Trainer in Global Problem Solving & Waste Reduction, Standardized Work and Kaizen Events. Mike is co-author with Jeff Liker of Toyota Culture: The Heart and Soul of the
Toyota Way, the biggest new contribution to the body of Lean knowledge in many years.
|
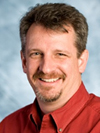 |
|
Jerry M. Wright, P.E.
Mr. Wright joined DJO in 1997. DJO is a global medical device manufacturer with annual revenues of $1 billion. DJO has operations in 18 countries and sells products in more than 70 countries. Since joining DJO, he has held leadership positions in quality, engineering and operations. He is currently the Vice President of Lean and Enterprise Excellence at the company’s headquarters in
Vista, California. At DJO, he was one of the key change leaders that helped to introduce lean thinking and transformed the company from a traditional batch and queue manufacturer to
a world-class, lean enterprise. During his tenure as the Director of Operations for Vista, the operation was honored as one of the Industry Week Top Ten Best Plants in North America
in 2005, and awarded 2006 Shingo Business Prize Recipient for Excellence in Manufacturing. The Product Development Management Association (PDMA) awarded DJO its 2005 Outstanding
Corporate Innovator (OCI) Award.
Mr. Wright holds a Bachelor of Science degree in Mechanical Engineering from Arizona State University and a Master of Business Administration degree from the University of Phoenix. He is a
licensed Professional Engineer in the State of California and the holder of one U.S. patent.
Mr. Wright is a current Shingo Prize Examiner, a 2007 Malcolm Baldrige National Quality Award Examiner and is the President of the West Region of the Association for Manufacturing Excellence
(AME). He is the lead instructor for the Lean Enterprise certificate course at University of California at San Diego. For the last 5 years, he has been the Chairman of the Southern
California Lean Network, an association of more than 50 companies across Southern California and northern Mexico that share best practices in lean, excellence and continuous improvement.
|
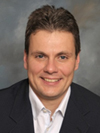 |
|
Steve Burns
Vice President Supply Chain and Operations, Avery Dennison Office Products
As Vice President of Supply Chain and Operations, Steve Burns runs Avery Dennison's Office Products global supply chain, procurement, manufacturing and logistics organizations.
Avery Dennison is recognized as an office products industry leader in delivering high quality products and superb customer service. Previously as VP of Operations, Office Product
North America Steve was responsible for overseeing the US manufacturing operations for the office products business. In this capacity, Steve was instrumental in bringing in the principles
of lean manufacturing and six sigma, which led to breakthroughs in the operations ability to quickly service a complex set of finished goods SKU's while driving costs and inventories down
each year. During these years, the office products division at Avery has received many external customer recognition awards for excellence in Supply Chain. Steve personally received the
2008 Avery Dennison Corporate Leadership awards for Enterprise Lean Sigma as well as Organizational Development. Prior to Avery Dennison, Steve spent time consulting in the engineering
field and 7 years with International Paper holding various roles in engineering and operations.
Steve holds a Bachelors degree in Electrical Engineering from Princeton University.
|
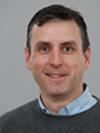 |
|
Robert Martichenko
Robert Martichenko is the Chief Executive Officer of LeanCor, LLC. LeanCor delivers Lean training, consulting, third party logistics and supply chain services to organizations embracing Lean and Operational Excellence in order to eliminate organizational waste.
Robert has years of supply chain, logistics and Lean implementation experience. This experience includes multiple Lean Supply Chain implementations supporting successful organizations including Toyota Motor Manufacturing.
Robert authored the books "Success in 60 Seconds" and "Everything I know about Lean I Learned in First Grade"; He also co-authored the logistics management book "Lean Six Sigma Logistics" published by J. Ross Publishing and co-authored the workbook "Building the Lean Fulfillment Stream" published by the Lean Enterprise Institute.
Robert complements his professional experience with a Bachelor Degree in Mathematics from the University of Windsor, an MBA in Finance from Baker College and is a trained Six Sigma Black Belt.
|
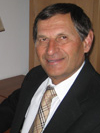 |
|
Roy Vasher
General Manager, Information Systems, Toyota Engineering and Manufacturing North America (retired), and co-author of Toyota Supply Chain Management.
Mr. Vasher developed deep insight and experience on how to integrate Information Technology to support Lean processes by serving as General Manager, Information Systems,
Toyota Motor Manufacturing North America. He has strong expertise in leading Supply Chain innovation in a Lean supply chain through development of robust processes supported by
intelligent use of technology for faultless implementation.
Roy was instrumental in streamlining and integrating Toyota’s North American and European Vehicle Supply Chains to reduce Order-to-Delivery lead-time and optimize vehicle
inventory—leading the industry in these innovations. He has an excellent knowledge and understanding of all Information Technology functions in a Lean environment.
He planned and directed the formation of two new Information Systems organizations, Toyota Motor Manufacturing headquarters, North America and the Toyota Manufacturing Kentucky plant
in Georgetown, KY.
|
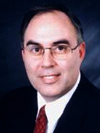 |
|
Dave Graham
Dave Graham started applying lean concepts while working in Toyota Motor Sales' North American Parts Operations Division. During his 17-year tenure, Dave has worked with the Distribution Operations, Sales, Transportation, Procurement, Supplier Development, Retail Operations, Information Systems, and Human Resources departments to implement JIT principles and Lean methods within Toyota's North American Service Parts supply chain. He currently assists companies implementing lean through Lean Quest, LLC.
|
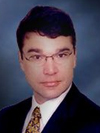 |
|
Alan Noss
Prior to founding Lean Quest, Alan worked for 13 years in the Service Parts Logistics Division of Toyota. During his tenure, he has been responsible for on going training, development, and implementation of Lean methods throughout the supply chain. Alan received top honors at 1997 North American Kaizen Conference and was selected to represent North America at 1998 Kaizen World Cup in Japan. Major projects highlights for which he was responsible included:
Managed configuration and quality control of advanced planning software for Toyota's B2B internet spin-off (iStarSystems).
Led two distribution centers in the implementation of Pull System and Lean concepts to achieve operational efficiencies. Trained operations management in the development of strategies and plans for implementing lean concepts resulting in productivity gains of 25%.
Implemented the first regional rollout of JIT deliveries to the dealership level. This resulted in shorter order lead times, reduced dealer inventory levels, and improved dealer operational efficiencies generating annual savings exceeding $250,000 per dealership.
Managed a project to design and develop the operational procedures for a new distribution center utilizing Lean methods and an automated warehouse control system. This was accomplished in Toyota's most automated distribution center in the world. This included the integration of material handling equipment into operational processes.
|
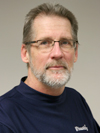 |
|
Jeff Hermanson
Jeff Hermanson, Executive Vice President/Vehicle Operations, The Braun Corporation. Jeff is responsible for ensuring that Braun provides the highest quality wheelchair accessible vehicles, overseeing both lowered floor minivan and paratransit van production. He is accountable for planning vehicle production capacity to ensure the Company's long term capability to meet market needs. Within this role, he is also responsible for LEAN implementation throughout Braun. Jeff has 30 years of diverse experience within the Company, having held management positions in Engineering, Purchasing, and Advertising, as well as coordinating plant layout and construction. He also served as Division Manager for Independent Mobility Systems and Crow River, which were two Braun acquisition facilities. Jeff attended Purdue University, and before joining Braun worked in an engineering capacity for Winamac Steel Corporation.
|
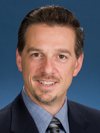 |
|
Mike Schober
Mike Schober is corporate manager of Supply Chain Strategy for North American Parts Operations (NAPO), a division of Toyota Motor Sales (TMS) U.S.A., Inc.
Schober is responsible for North American service parts and accessories supply chain strategy and design for Toyota, Scion and Lexus. In this capacity, he is responsible for the design and execution of supply chain strategies to maximize customer value, build an efficient infrastructure, leverage global logistics, synchronize supply with demand, and optimize profitability. Additional responsibilities include oversight of NAPO's national environmental, hazmat, and safety programs, industrial engineering function, dealer parts call center, and information systems planning and application. In addition to the above duties, Schober is also responsible for the Organizational Development and Kaizen Departments within NAPO. In this capacity, he is charged with promoting and inculcating the principles of the "Toyota Way," TPS, and Total Quality Management (TQM) to a motivated workforce of more than 1,900 associates across NAPO. This includes oversight of the TPS Certification Program, which builds strong technical expertise in the understanding and application of Toyota Production System principles.
After joining Toyota in 1987, Schober has held a variety of operations management positions with TMS. He was production manager for Toyota’s vehicle accessorization plant in Long Beach California, where he vigorously applied Toyota Production System (TPS) principles to achieve efficient assembly line processes. Recently, Schober oversaw the largest distribution center operation in North America for Toyota, the North American Parts Center in Ontario, California (NAPCC). In this capacity, he directed a large and dynamic workforce in providing service parts and accessories to six North American distributors, two private distributors, 12 regional distribution centers, Toyota Motor Corporation and Toyota Motor Manufacturing Europe. While under his direction, NAPCC achieved the prestigious Voluntary Protection Program Star (VPP) status from Cal/OSHA for demonstrating exemplary safety performance, as well as "WRAP of the Year" recognition from the California Department of Resources Recycling and Recovery for outstanding waste reduction efforts.
Schober holds a M.B.A. degree in Marketing from Loyola Marymount University, and a Bachelor of Arts degree in Economics from the University of California, Los Angeles (UCLA).
|
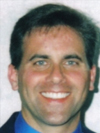 |
|
Ron Covelli
Manufacturing Manager, Moog Inc. Aircraft Group, Torrance Operations
In his current capacity, Ron's focus is maximizing utilization and efficiency of personnel and equipment to provide optimum productivity at the least possible cost and originate long-range planning of shop and productivity improvements. He has transitioned the manufacturing operations at the Torrance facility from an MRP based to a continuous flow demand driven system.
Ron has years of experience in process improvement, development and deployment at Moog Inc. domestic and international locations in Teaming, Lean, and Process Variation Reduction (Six Sigma). He has co-developed and is a company instructor of Moog's Lean Certification Training, Structured Team Training, and Six Sigma Yellow Belt Training. He has been a deployment lead for a large scale transition of the Assembly and Test and Office Areas from supervised departments to self-directed work groups. Ron has instructed at the collegiate level, and was recognized in 2004 by The Career Resource Center and LEAP (Learning Experientially in an Academic Practicum Internship Program) at the University at Buffalo School of Management for his contributions to the professional development of UB interns who worked for him in supply chains and operations management.
Ron holds a Bachelor of Science degree and Master of Science degree in Industrial Technology from the State University College at Buffalo, and is a certified Six Sigma Master Black Belt from Breakthrough Management Group (BMG).
|
Back To Top
|
|